・溶接ワークの位置決めに三次元測定機を活用
・車種毎の専用治具を使わず
ロボットでワークの位置決め~溶接を行うシステムを構築
アイシンシロキ株式会社の前身は、1946年創業の白木金属工業株式会社。東京日本橋にあった老舗百貨店「白木屋」の子会社として設立されました。当初は鍋や釜の製造からのスタートでしたが、現在は自動車に搭載されているドアフレームやウィンドレレギュレータなどを製造・販売、国内外の拠点で展開しています。
主要取引先にはトヨタ、日産、スズキ、本田技研、ダイハツ、いすゞ、三菱、SUBARUなど国内ほとんどの自動車メーカーが並びます。1枚の金属板から中空の部品を作り出す「ロールフォーミング」は難しい曲面加工を必要としますが、アイシンシロキの技術力は高く、長年評価を受けてきました。
しかし近年の自動車業界の技術革新はスピードが上がり、部品加工について早く・安く・高品質なものを提供するのはもちろん、多種多様な車種への対応、製造技術の工夫が求められています。物理的な加工技術の向上だけでなくDXやIoTとも連携した新しい加工プロセスの開発や設備が必要です。
そこでアイシンシロキでは、量産を終えた旧モデルのドアフレーム加工を端緒に、レーザー型三次元測定機とロボットを活用した「溶接治具レス化プロジェクト」を立ち上げました。さまざまなデバイスから選択いただいたのが、東京貿易テクノシステムの「LeicaレーザートラッカーAT960」「Leica AS1スキャナー」「Leica T-Mac」と3D計測ソリューション「PolyWorks Inspector™」です。
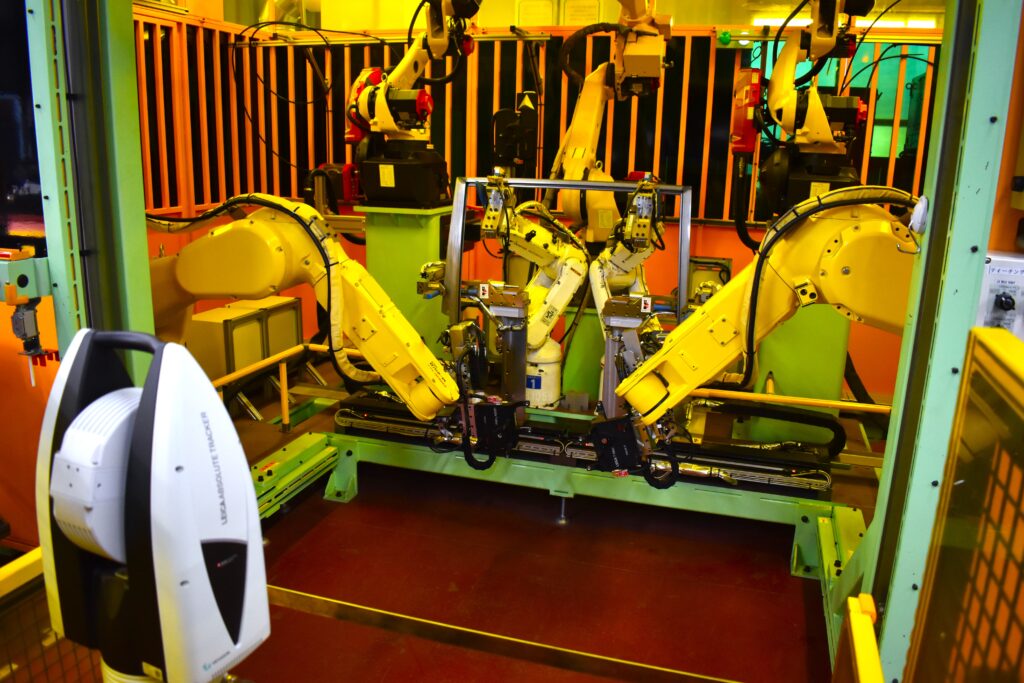
Leica レーザートラッカーAT960とLeica T-Macで計測を実施している様子
導入は2021年7月ですが、その1年以上前から東京貿易テクノシステムのほか3社がチームとなって新プロジェクトを支え、ロボットを使った治具レス化システムが実現しました。本格稼働は2023年春から始まっています。今回はプロジェクトの経緯やデータ応用について詳しく伺いました。
- 課題
-
- 量産後の旧モデルの固定式溶接用治具は長期保管が必要で、場所を取る
- 修理対応などの旧モデル部品加工は少量で手間がかかり利益が出にくい
- 車種ごとに細かな位置合わせが必要な加工作業、いずれ全自動化したい
- 解決
-
- 三次元測定機を使って部品同士の空間を調整、固定式溶接用治具を不要に
- 技術者の属人的な能力ではなく、測定した数値をベースに作業を効率化
- 三次元測定機・解析ソフト・ロボットを組み合わせて全自動化を実現
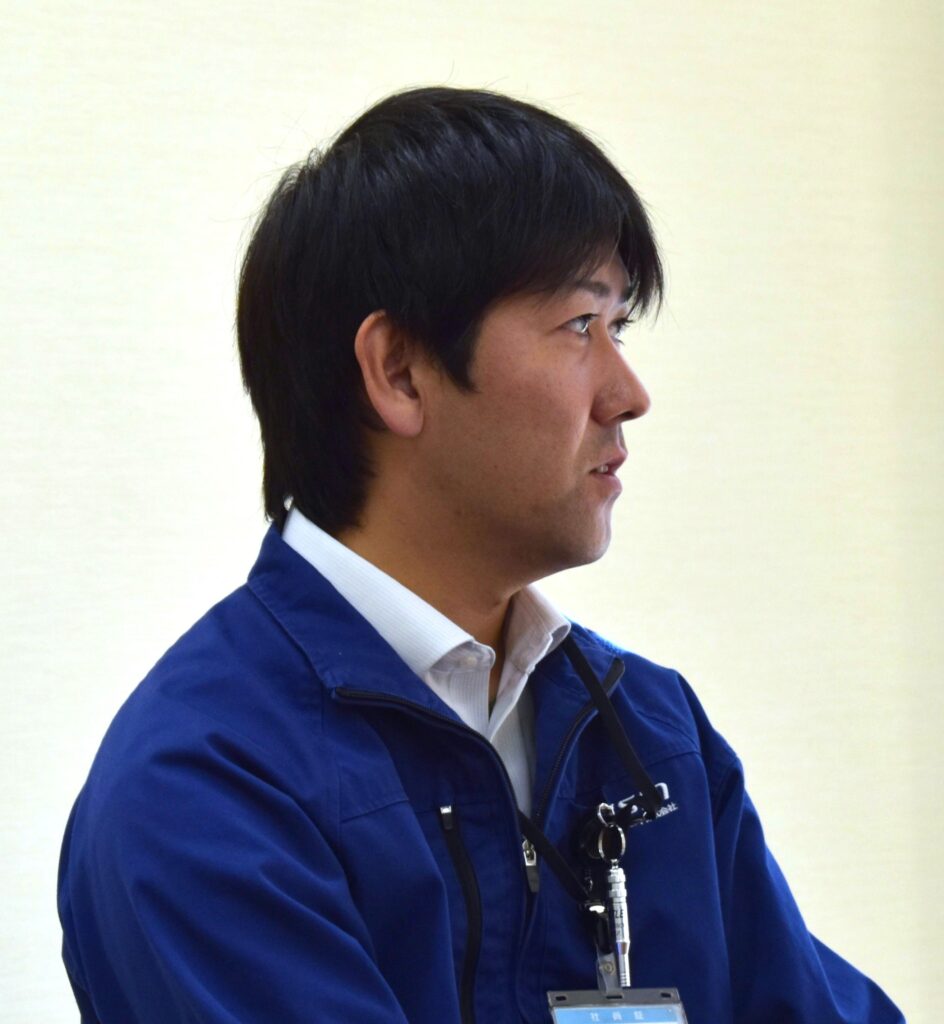
外装部品生技部 ドアフレーム開発室 内山さん
自動車のサイドドアに付けるドアフレーム(窓枠)の製造設備やラインを開発する業務に従事。1車種ごとに形状が異なるフレームを、いかに効率よく・安く・高品質で作るかを研究し、3Dスキャナとロボットで構築した治具レス溶接システムを実現させた。
品質測定ではなく、加工プロセスの空間計測に活用
今回は「LeicaレーザートラッカーAT960」をはじめ、非接触で精密に測定できる「Leica AS1スキャナー」「Leica T-Mac」まで導入いただいています。どんな業務で使われているのでしょうか。
私たちの使い方は特殊かもしれません。通常なら製品完成後の品質測定に使われることが多いと思うのですが、弊社では部品溶接プロセスでレーザートラッカーを導入しています。
自動車のドアフレームは、数種のワークが溶接によって組まれています。ワークは車種ごとに細かく形状が変わり、溶接する角度・位置はその都度調整しなければいけません。間違いなく溶接するため、現場では長年にわたって各々の車種専用の固定型の治具を使用していました。ワークを治具に乗せて固定し、その上で溶接加工をしていたんです。
ただ、この治具は車種毎のドア1枚1枚に対して必要で、サイズも大きいです。ある車種の量産が終了しても修理品等のサービスパーツ対応で、生産する必要があるために保管が必要で、少量受注があるたびに引っ張り出して調整・生産していました。車種が増えるたびに治具が増えるので、どの企業でも保管は課題になっているのではないでしょうか。
私たちはその問題を解決するため、車種専用の固定式治具に頼らない新しいシステムを構築しようと考えました。そこでカギとなったのが三次元測定機の応用です。
どのように使っているのか、詳しく教えてください。
まず、溶接したいワークをロボットハンドや汎用治具に把持します。ここで三次元測定機を使い、ワークのCADデータによる寸法値・トラッカーの測定値を照らし合わせて部品同士の空間座標を計測します。この数値を使ってワークの位置決めをすれば、必ずしも車種専用の固定型の治具に頼らなくても毎回正確な角度・位置で溶接できるわけです。
車種専用の固定式治具でも経年で摩耗したり部品交換したりするので調整は必要ですし、作業者により調整のレベルも異なります。
しかし測定値から割り出した座標をベースにすれば、治具や環境のコンディションに左右されず、数値を元に計算する性質上、作業者の習熟度も影響しません。ロボットにデータを渡して位置決めから溶接までを自動化すれば、車種専用の治具がない分、大幅な効率化を図れます。
とても便利なシステムが構築できるんですね。
この仕組み自体は、以前からいろんな企業が発想して挑戦してきたと聞いています。ただ、いくつかの課題があってなかなか実現に至りませんでした。
第1に、三次元測定機の精度の問題です。デバイスの特徴として「狭い範囲は高精度に測定できるが、広範囲だと精度が落ちる」のは避けられません。ドアフレームのワークは比較的大きい部類なので、どうやって精度を担保するかが課題です。
第2に、データを受け取るロボット側の精度の問題です。数値で指示をすることができてもロボットの動きを私たちが求める範囲以内の誤差に収めるのが難しい。使い続ければロボット自体のギアの摩耗が発生するため、位置ズレなども考慮する必要があります。ロボットが最初から高精度な位置決めができればいいのですが技術的にはとても高度です。
技術を持っているいくつかの企業に相談しましたが、どこからも「そんなのできませんよ」と断られてしまいました。しかし1社だけ「やってみましょうか」と前向きになってくれた企業がありました。それが東京貿易テクノシステム様だったんです。
柔軟なアイデアで課題解決策を提案してもらった
1社だけ、前向きな回答だったんですね。
どんなシステムを構築したいかご相談し、レーザートラッカーと「PolyWorks Inspector™」の組み合わせを紹介してもらいました。当時はまだレーザートラッカー購入前だったので、弊社は顧客ともいえない立場です。それでも親身になって全力で方法を模索していただいたのは本当にありがたかったですね。
第1の課題については、広範囲を高精度で計測できる「LeicaレーザートラッカーAT960」と小型のカメラ式3Dスキャナの併用を提案いただいて採用しました。両者のデータを計算することで、レーザートラッカー座標系で全ての3Dスキャンデータを表示することができます。カメラ式3Dスキャナは東京貿易テクノシステム様の製品ではないので申し訳ないと思ったのですが「精度が上がるなら」と言ってくださり、おかげで私たちも自由度が上がって扱いやすくなりました。
データの扱い方についても、「PolyWorks Inspector™」を使って、元のCADデータと測定点群を合致させる方法を提案くださったのは東京貿易テクノシステム様です。専門知識がない私たちでも使えるよう、細かい設定のコツを教えてもらいました。
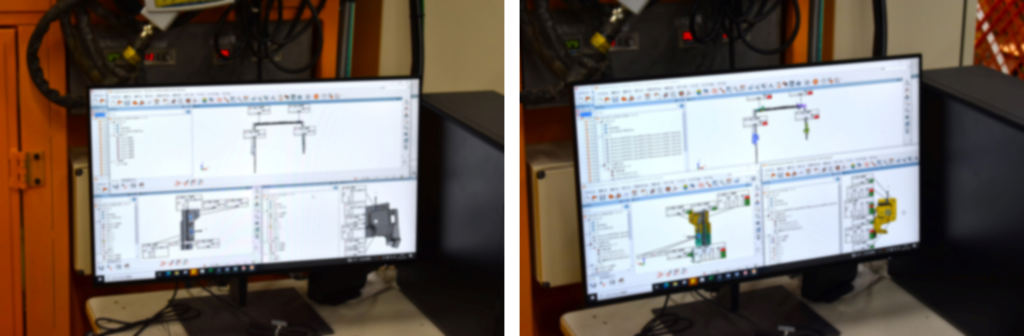
現場に合った具体的な解決策が提供されたのですね。
そうですね。ロボット制御については他企業にも声をかけていただいて、5社によるチームでプロジェクトを進めました。東京貿易テクノシステム様の三次元測定機と解析ソフト、ROBOSHIN様のロボット制御技術、タマディック様による構想提案と連携、タクトシステム様の汎用治具や設備などのサポートがあり、本技術の実現があります。
第2の課題だったロボット制御に関しても、ROBOSHIN様の方で、レーザートラッカーを活用した高精度な位置決めプログラムを組んでいただき、ロボットの高精度な位置決めが可能になりました。このチームでなければ難しかったと思っています。
難しい開発プロジェクトも、楽しいチームで進められた
レーザートラッカー、非接触・有接触のオプション、全自動化システム導入など、予算も場所もかかるプロジェクトですが、社内での意見はありませんでしたか。
システム構築を検討していた2020年当時、前社長が「お金はいくらかかってもいいから挑戦してみろ」と後押ししてくれました。また今の社長と役員も引き続き強く応援してくれています。変化していく自動車業界において必ず新しい技術が求められること、汎用性の高い技術は他の量産ラインにも応用できることを見越していたのだと思います。
2023年4月からは本格稼働し、旧モデルの補給生産を始めています。物理的なモノを調整する工程から数値計算による調整を行う工程に変わるので、現場の皆さんに理解いただきながら、一緒に車種の追加・生産活動を進めているところです。今後は必ず生きてくる技術なので変革の過渡期として理解してもらっています。
これからの技術として導入を決断されたんですね。
はい。それに加えて、今回チームの皆さんで楽しんで開発を進められたのは大きな経験でした。大きな開発課題がある案件は、通常はどうしても後ろ向きになってしまったり、失敗したらどうしようと萎縮してしまったりします。このプロジェクトでは皆で開発のアイデアを和気藹々と検討して、エラーが出ても解決すればいい、できなければ他の方法を探せばいい、というマインドで進められました。

私自身、最初は「みんな無理だというなら無理かも、可能かどうか判断できるところまではやってみるか」くらいの気持ちだったんです。しかし今は、東京貿易テクノシステムの営業や技術の皆さん、他社の皆さんと話しながら試行錯誤を繰り返し、まだどこにもない新システムを構築できた達成感があります。
ほとんど知識も技術もゼロのところから教えていただきました。デバイスだけでなく解析ソフトについても知識が深いのは東京貿易テクノシステム様の強みだと思います。応用力とアイデアに大いに助けてもらいました。
このプロジェクトが始まった時期、経営者としての判断、それに東京貿易テクノシステム様、ROBOSHIN様、タマディック様、タクトシステム様との出会い、全てのタイミングが運命的だったと思います。どれ一つ欠けていてもできなかったというのは間違いないですね。
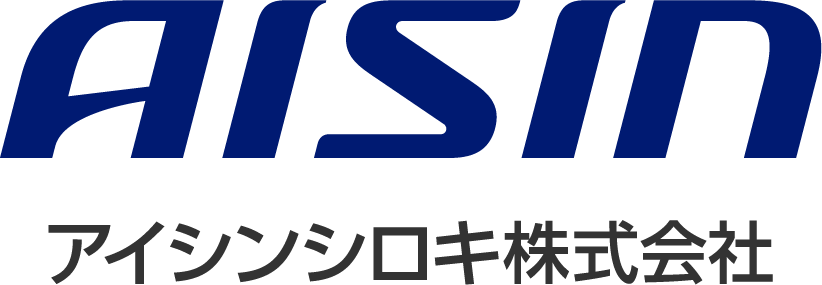
アイシンシロキ株式会社様
東京日本橋にあった老舗百貨店「白木屋」の子会社「白木金属工業株式会社」として1946年に創業、2023年に社名を「アイシンシロキ株式会社」に変更。現在は、ドアフレーム(窓枠)、ウインドレギュレータ(窓昇降装置)、ドアロック、モールディングなど、自動車用内装・外装部品の製造・販売を国内外で展開している。生産技術力とものづくり力を重視し、変化の激しい自動車業界に対応できるよう新たな技術開発にも取り組んでいる。
【この事例で紹介された製品】Leicaレーザートラッカー