こちらの記事は『トヨタ自動車株式会社様より2021年度「技術開発賞」を初受賞いたしました』の英語版です。
Tokyo Boeki Techno Systems Ltd. (TTS) received the “Technology Development Award” for the first time from Toyota Motor Corporation for the “Development of high-performance autonomous construction measurement technology by linking general-purpose equipment” in collaboration with TOYOTA MOTOR KYUSHU, INC. and TOYOTA PRODUCTION ENGINEERING CORPORATION. The “Technology Development Award” is given to suppliers who have promoted manufacturing with innovative technology. It is one of the most prestigious Toyota technology-related awards, and TTS’s technology was recognized by “TOYOTA” with this award.
Award Details
Problem
During sampling checks of completed vehicles, workers were manually measuring 500 to 900 spots. At that pace, the best they could do was to inspect two vehicles a day. The number of vehicles inspected was too small for effective tendency management.
In addition, the creation of a conventional automatic construction measuring facility would require an investment of more than 100 million yen and a large space for measurement.
Solution
TTS’s autonomous construction measuring system, which combines measuring instruments, collaborative robots, and AMR in a program, requires no isolation from human workers.
The ARM* allows the robot to move freely, requiring only about half the space of other companies’ facilities and about one-third the investment cost. *AMR: Autonomous Mobile Robot
System configuration
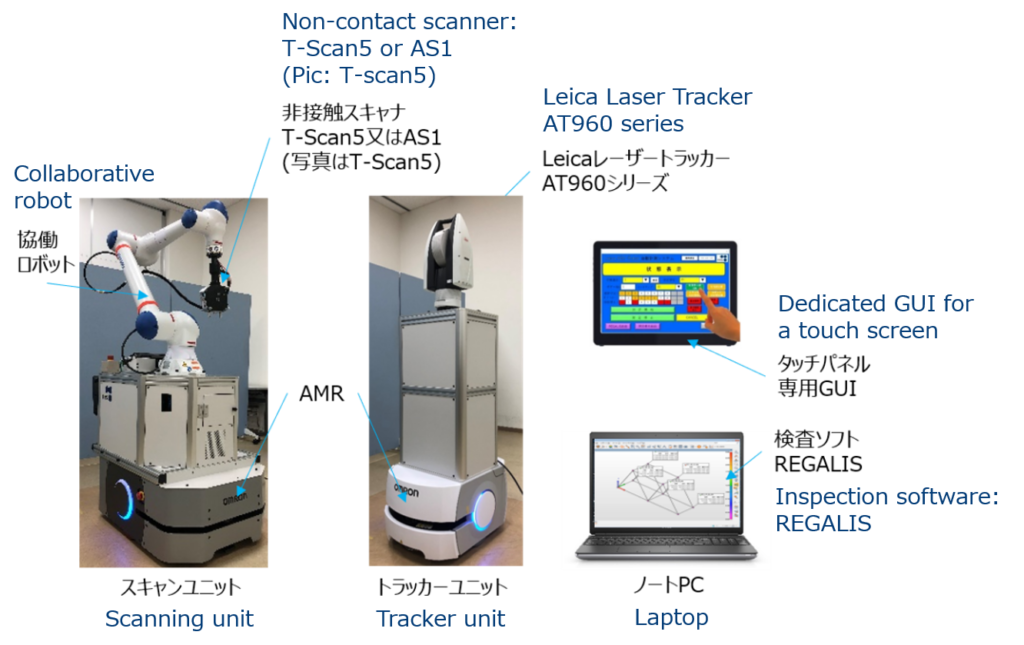
Measuring scene
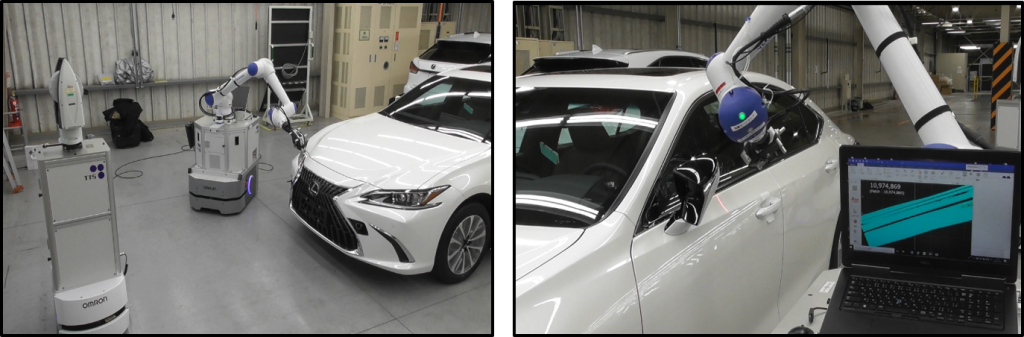
A system which is operated by a program that links all of the measuring machines, collaborative robots, and AMRs
The following 3 technologies are used:
- AMR position compensation technology using Leica AT960 laser tracker and T-Scan5 function
AMR stopping accuracy is ±100 mm. A deviation of 100 mm may cause a collision between the scanner and the vehicle during measurement. Therefore, the scanner position is detected and calibrated in the AMR to achieve a stopping accuracy of ±10 mm.
- Robot compensation technology
If the position of the parting line measurement deviates even slightly from the position simulated offline, the data may be lost and measurement may not be possible. Therefore, the robot compensates for the ±10 mm discrepancy which cannot be fully compensated by AMR to bring the position closer to the simulated one.
- Tracker changeover (reference replacement) technology
The tracker and scanner must always be within 5 meters of each other and the scanner must be visible from the tracker. In order to measure the entire circumference of the vehicle, the tracker must be repositioned according to the robot’s position. To do this automatically, the tracker is moved based on the scanner’s position information.
The important point is that the vehicle and robot are always in the same position and measurement can be done on the same trajectory, regardless of the vehicle’s position. This enables highly accurate and safe autonomous measurement without colliding with the vehicle.
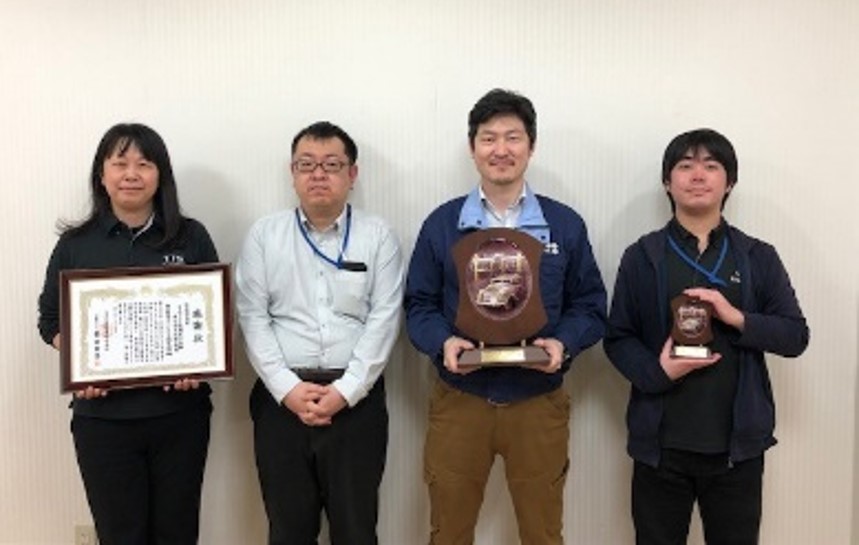
TTS will continue to develop and provide solutions that incorporate state-of-the-art technologies and concepts, and boldly take on the challenge of solving ever-changing problems faced by customers and markets. With the goal of creating a sustainable society, TTS will make a lasting contribution to society through our business and what we can do as a company.
For any inquiries, please contact us via mail icon below.