The reverse-engineering solution that enables true interoperability between digitized polygonal models and your CAD/CAM applications
Product Description
PolyWorks|Modeler™ is a comprehensive reverse-engineering software solution that allows extracting optimal CAD entities—curves, surfaces, parametric sketches, and prismatic features—from polygonal models of digitized parts to serve as the starting point in your professional CAD modeling solution.
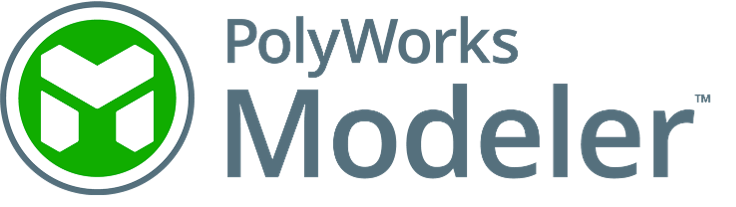
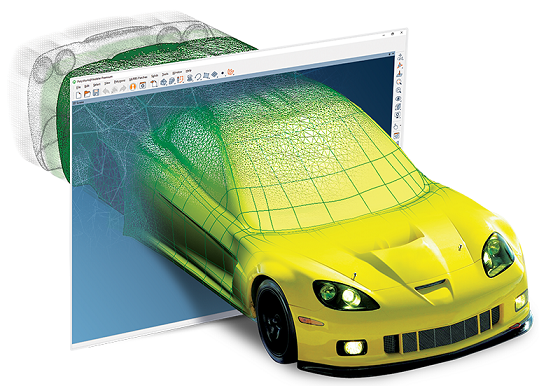
Product Features
Polygonal Modeling
The first step in a reverse-engineering workflow consists in transforming digitized point clouds into surface-based polygonal models, also called meshes. Polygonal models are more compact, more accurate, and less noisy than raw point clouds and are directly handled by industrial applications such as milling, 3D printing, and aerodynamic simulation.
Create polygonal models of digitized parts in real time
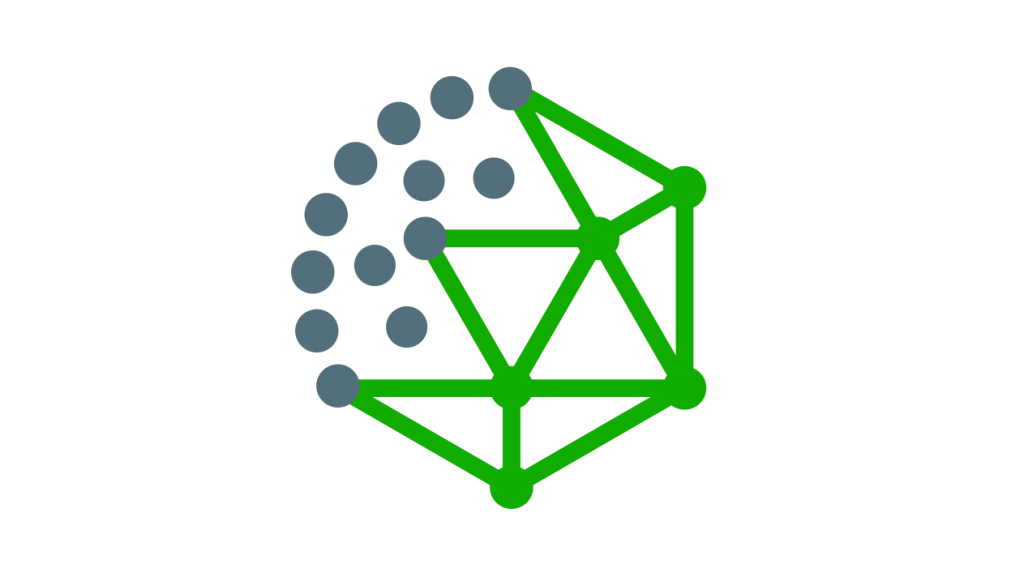
Repair and optimize imperfectly digitized geometry
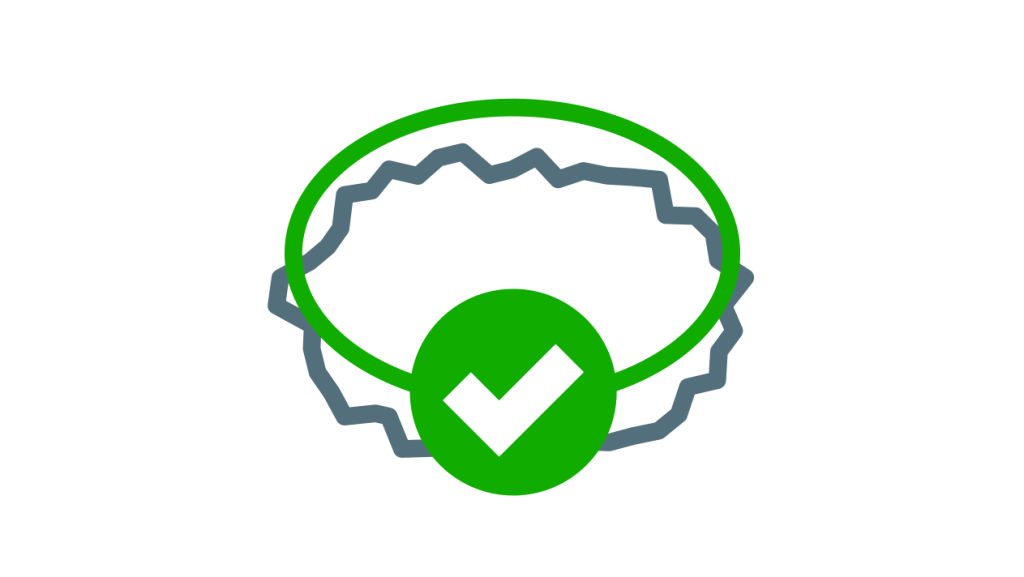
Apply CAD operations to polygonal models
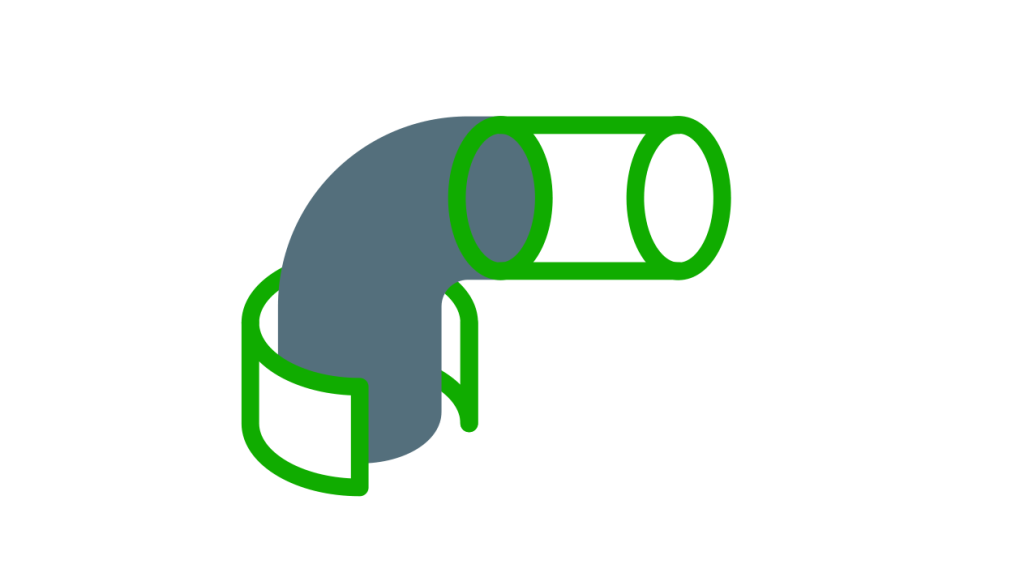
Surface Modeling
NURBS surfaces are lightweight representations of simple geometric features and complex organic shapes that are commonly used to replicate and transfer the surfaces of polygonal models built from digitized point clouds to CAD/CAM software. PolyWorks|Modeler offers an intuitive curvature-driven NURBS surfacing approach that generates superior surface continuity, smoothness, and accuracy.
Create curve networks and surface patches
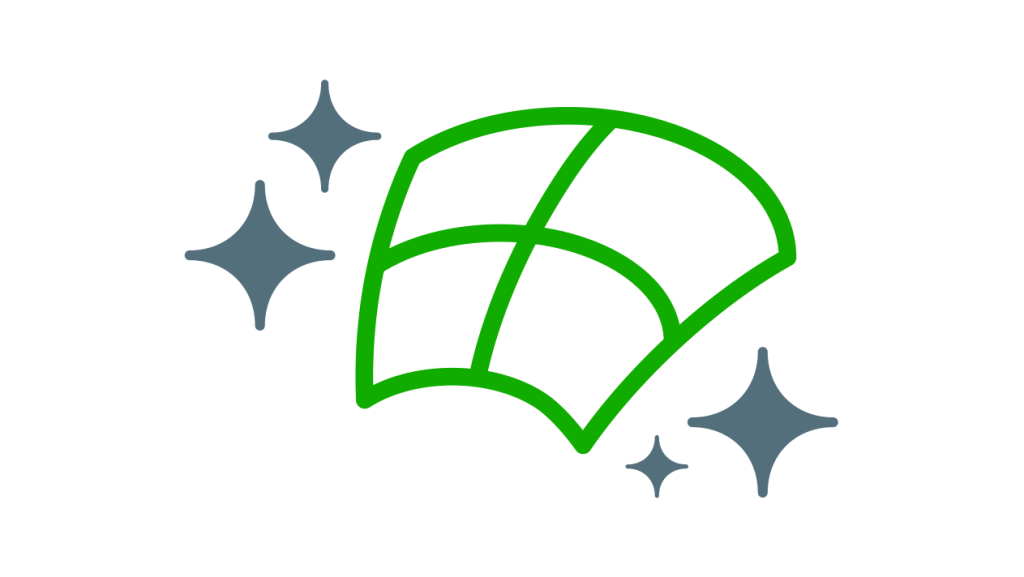
Generate accurate, smooth,and continuous surfaces
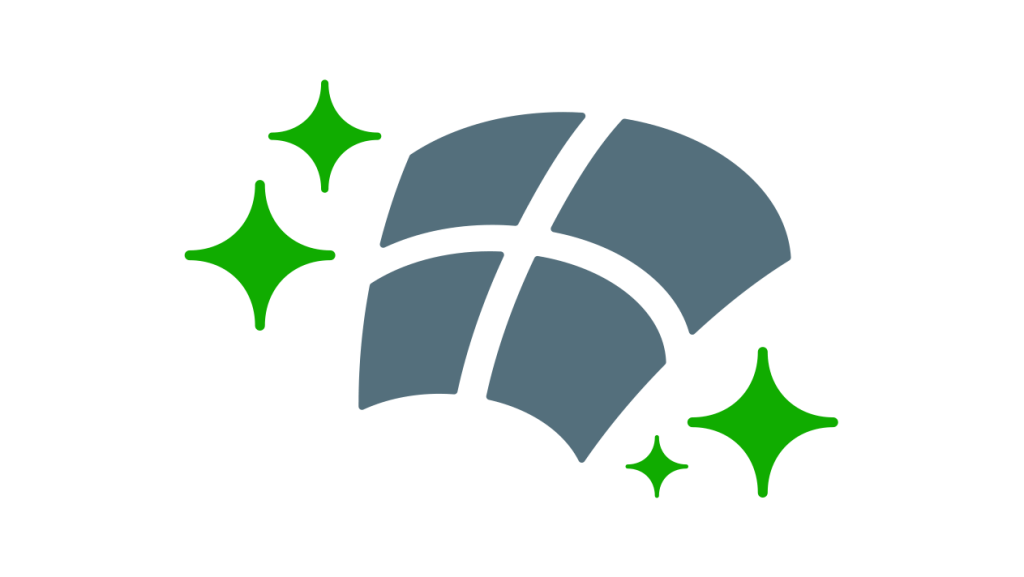
Transfer surfaces to your CAD/CAM solution
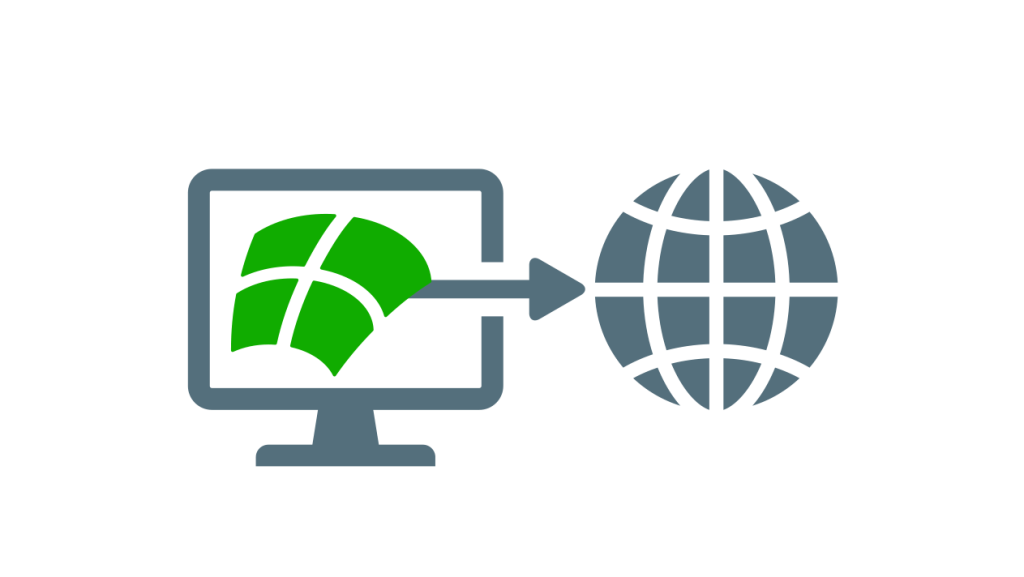
Solid Modeling
A fundamental building block in a solid modeling workflow is the parametric 2D sketch. It is used to create solid base features by performing Extrude, Revolve, Sweep, and Loft operations. PolyWorks|Modeler optimizes the extraction of geometric entities on digitized polygonal models to create parametric 2D sketches that serve as the starting point in your CAD solution for generating parametric, associative, and fully editable solid 3D CAD models.
Create sketches from digitized models
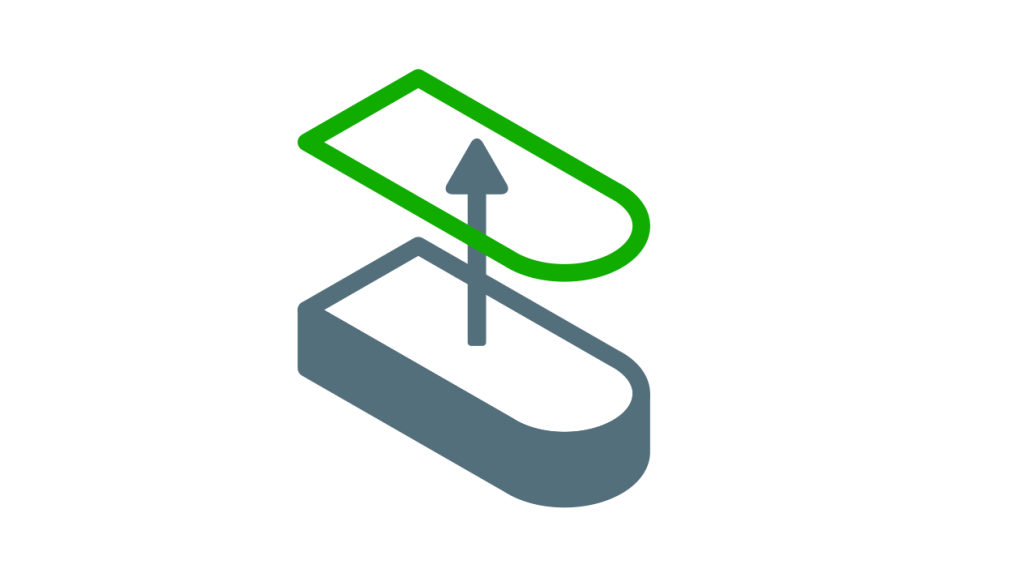
Create sketch entities and dimensions
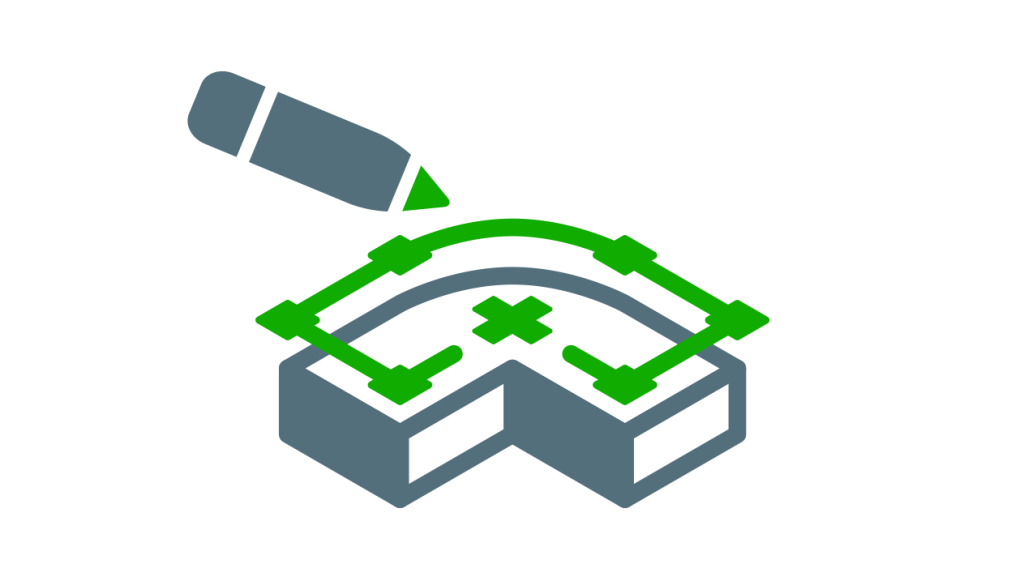
Transfer PolyWorks sketches to your CAD solution
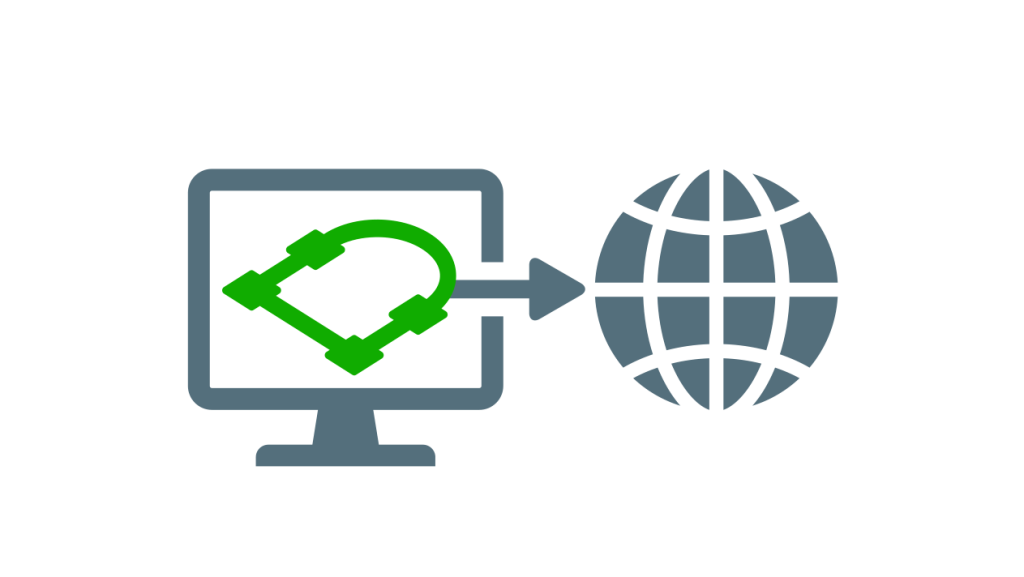
PACKAGES
Point cloud digitizer for portable metrology | |||
---|---|---|---|
Single-point measuring device for portable metrology | |||
Real-time quality meshing and offline point cloud meshing | |||
Polygonal editing | |||
Parametric sketching | |||
NURBS surfacing | |||
One-year support/maintenance |