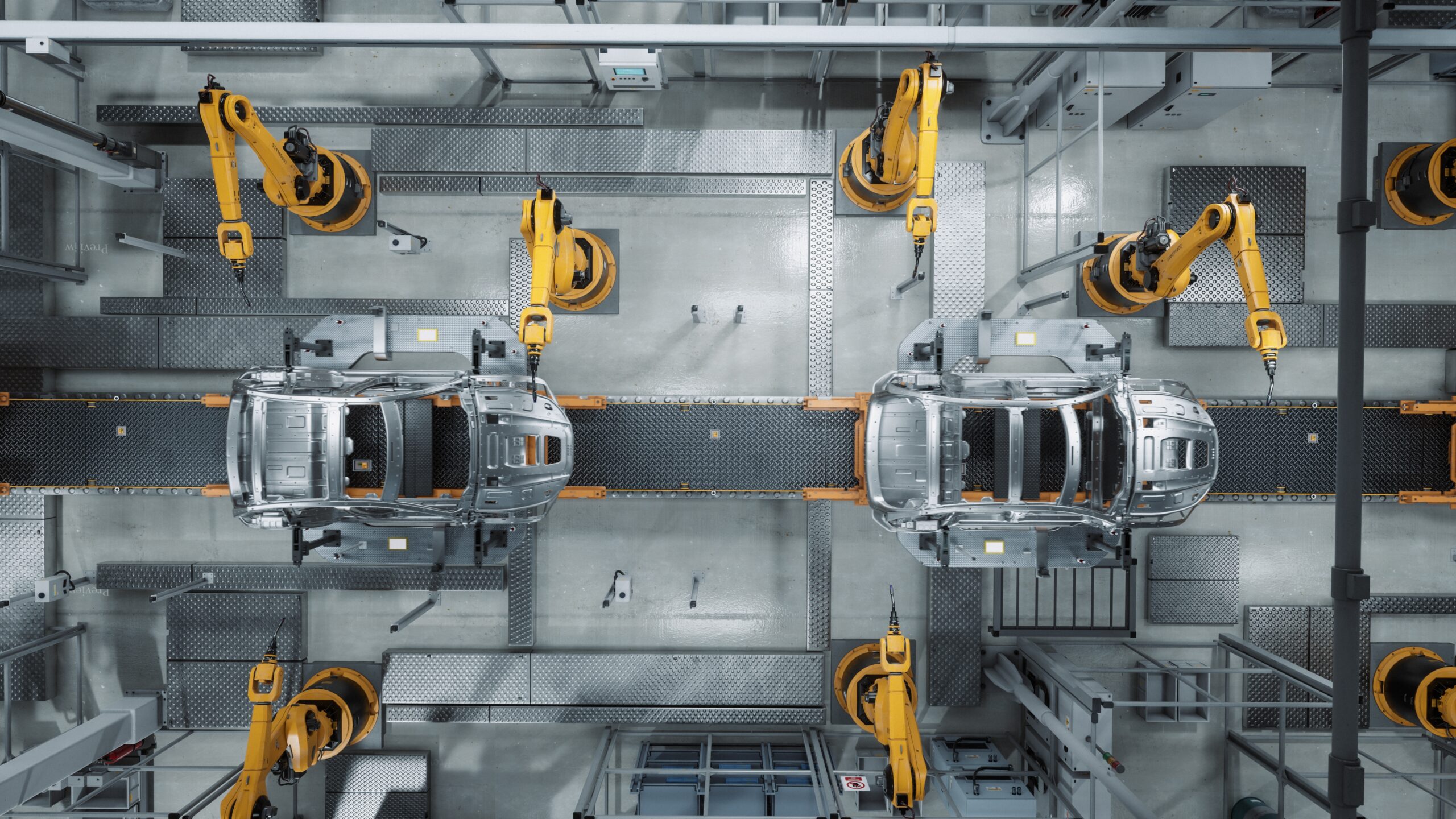
CoPick3D – 3D Vision Features for Full Automation and Unmanned Operation
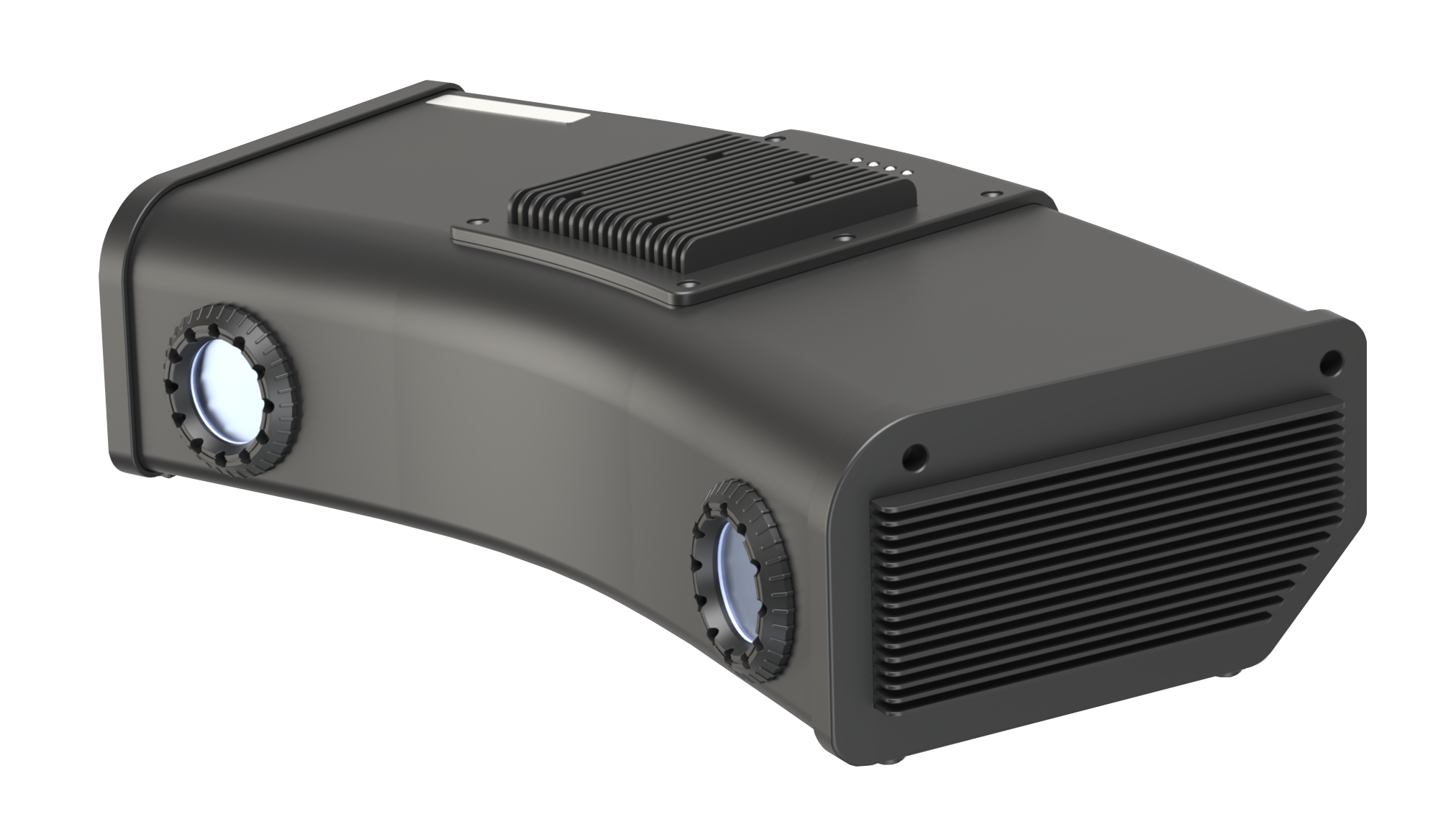
CoPick3D is a high-speed, high-precision 3D machine vision system equipped with an industrial camera, designed to support automated assembly and inspection processes with an accuracy of within ±0.5 mm. It offers rapid, wide-area scanning within seconds, enabling significant reductions in overall system configuration costs. The system utilizes structured light cameras to capture high-resolution 3D data, including color information, which seamlessly integrates with downstream inspection systems powered by deep learning and machine learning technologies. CoPick3D is highly adaptable to a wide range of industrial environments and provides a powerful solution for achieving fully unmanned automation.
Core Functions for 3D Vision Automation
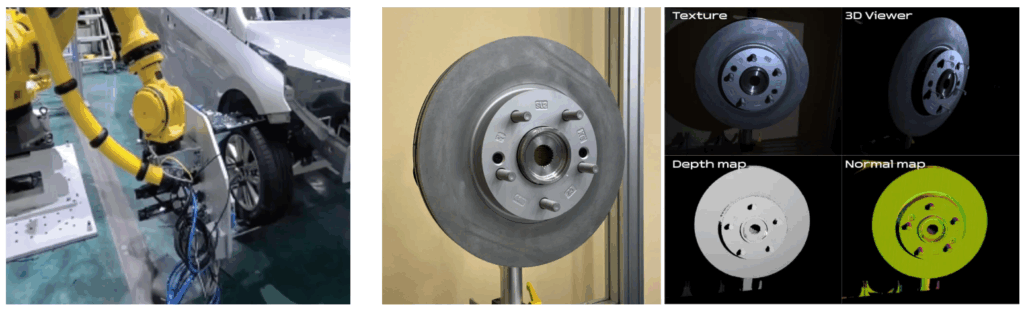
Precise Automation System
- Built on ±0.1 mm accuracy, the system enables reliable robot guidance with final positioning errors within ±0.5 mm, even in complex processes
- Enables stable part alignment and assembly without operator intervention
Real-Time Processing Capability
- Leveraging CUDA-based parallel processing, the system completes all tasks in under 1.5 seconds
- Enables rapid changeover and real-time response even in environments with high-mix, low-volume production
High Measurement Accuracy
- Industrial cameras using structured light technology can simultaneously recognize objects with varying colors and reflectivity
- Enables high-precision position estimation and quality inspection based on 3D point cloud data
Efficient Production System
- Provides optimization through the integration of hardware and software
- Contributes to reducing lead times across all processes and improving productivity
3D Robot Guidance with Industrial Cameras
Automated Windshield and Sunroof Installation System
The 3D machine vision solution based on CoPick3D enables high-precision correction of the vehicle body position — even when the body slightly deviates upon entering the assembly process ― by utilizing FineLocalizer, CLE’s proprietary robot guidance application software.
Additionally, errors and misalignments originating from the glass alignment machine and gripper are detected in real-time, allowing for highly accurate robot guidance that simultaneously accounts for the relative positions of the vehicle body and glass.
This solution integrates glass installation and quality inspection within a single system, ensuring stable quality throughout the entire process while enabling continuous quality monitoring.

Bolt Picking System
The system utilizing CoPick3D simultaneously detects up to n bolts randomly piled inside a container with just a single structured light scan, as specified by the user. It then guides the robot to sequentially and accurately pick the bolts for the nut runner’s cartridge.
Furthermore, it features User Preference-Based Bin Picking technology that adapts to uncertain conditions during picking—such as bolt thread damage or position shifts—according to user intent, maximizing the stability and consistency of the picking process.
Compared to traditional drum-type bolt feeders, this solution offers a more flexible working environment and superior adaptability. It effectively handles practical constraints in the field, including dummy capacity limits, diverse bolt types, and defective part sorting.
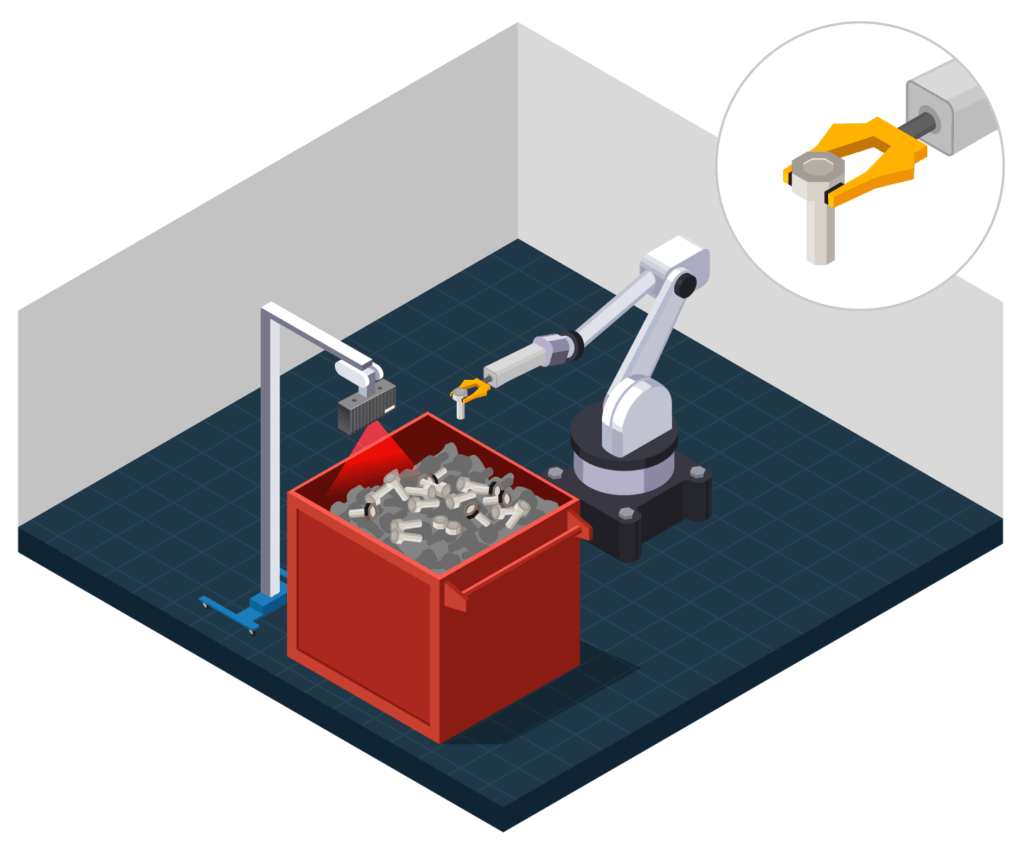
Irregular Wiring Connector Attachment & Detachment System
CoPick3D and FineLocalizer enable stable and high-precision automation of particularly challenging tasks such as the attachment and detachment of irregular wire cables and connectors in automated production processes.
A representative application is the full automation of connecting a test module cable—comprising three connectors used in electric vehicle power systems—in a precise sequence within a limited time frame.
By replacing manual operations traditionally performed by workers with robotic automation, this solution achieves highly accurate gripping and stable assembly, dramatically enhancing production efficiency.
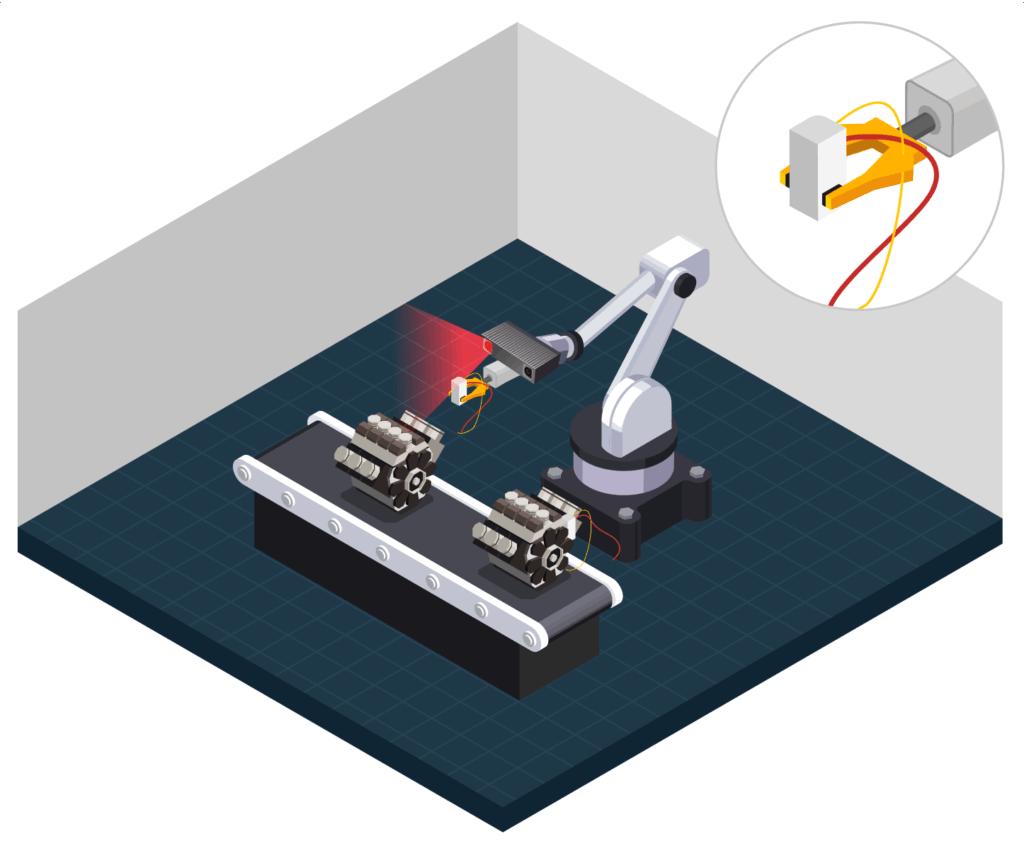
Automated Tire & Wheel Installation | Deep Learning Inspection
FineLocalizer offers CoPick3D’s dedicated hole and stud recognition technology, which leverages geometric constraints such as square, pentagonal, and hexagonal shapes to accurately calculate the entire wheel hub’s pose using information from only three holes or studs.
Additionally, CoPick3D features color texture-based capabilities, enabling integrated execution of automatic tire and wheel installation alongside heterogeneous inspections. This integration simplifies and consolidates multiple vision systems that were previously installed separately, significantly reducing equipment costs and installation space.
Furthermore, the technology employs deep learning-based high-precision object recognition to accurately identify tires and wheels regardless of type. It ensures error-free, high-precision installation according to vehicle-specific sequences (assembly order and specifications).
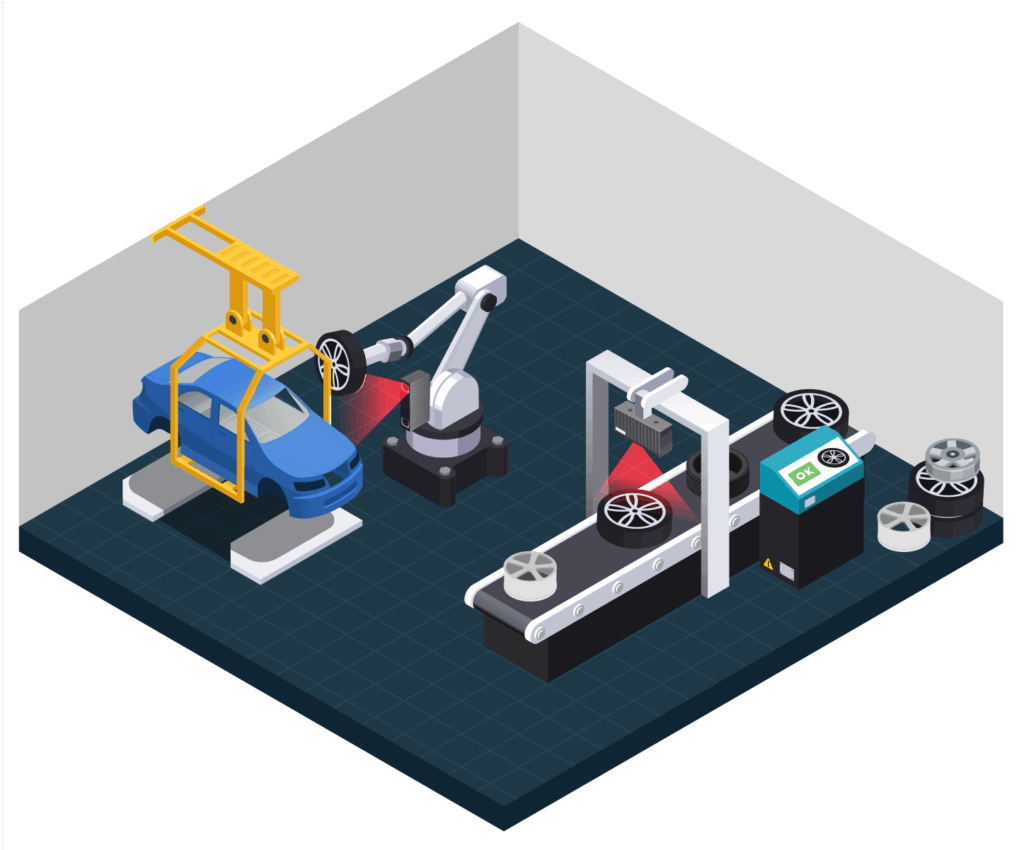
Inspection System Utilizing Structured Light Technology
FineLocalizer is a robot guidance application that achieves highly precise correction errors within ±0.2 mm and ±0.1°. It utilizes structured light technology to simultaneously scan both dark and bright objects.
Additionally, it features advanced inspection capabilities that accurately recognize irregular and complex shapes.
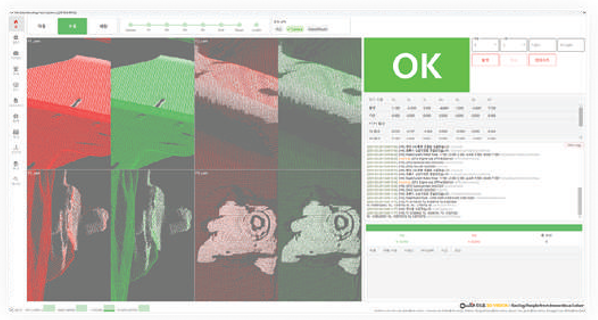
FineLocalizer for Headlining Auto Mounting
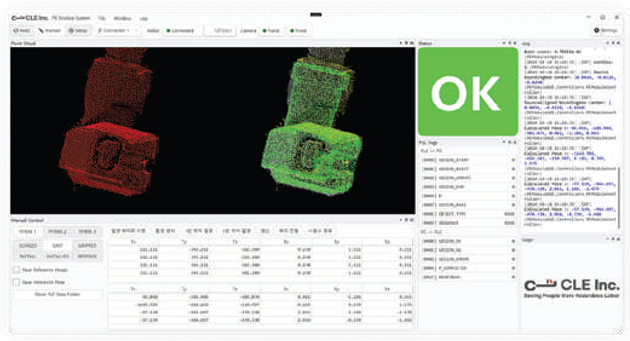
FineLocalizer for Wiring Cable Auto Mounting
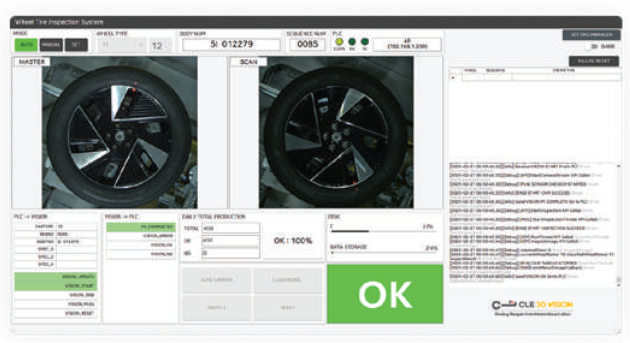
FineInspector for Wheel Type Recognition
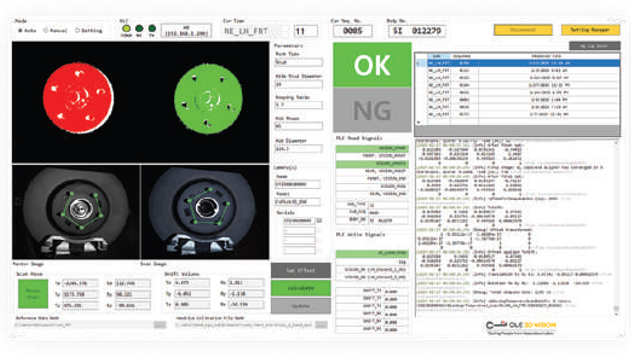
FineLocalizer for Wheel-Tire Auto Mounting
Learn More About 3D Machine Vision with Industrial Cameras
We provide detailed documentation covering specifications and other information on our process automation systems. Additionally, we welcome inquiries for demos, benchmarks, and more—please feel free to contact us.