- Mission
-
- Need to be able to do assembly of large structures such as a bridge on software to reduce the number of man-hours and adjustments on site.
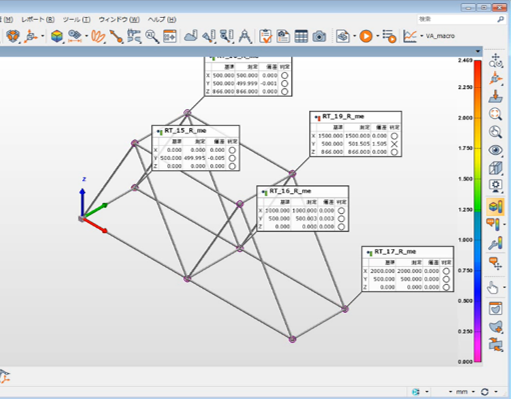
Solution
By measuring each part in 3D and performing virtual assembly on the software, errors and correction points can be identified in advance and necessary corrections can be made before actual assembly.
Proposal Contents
By scanning each part of a large structure in advance with high accuracy with a laser tracker and virtually assembling it on the software, it is possible to detect defects in the shape of the parts before actual assembly and correct them in advance, thereby reducing time and costs.
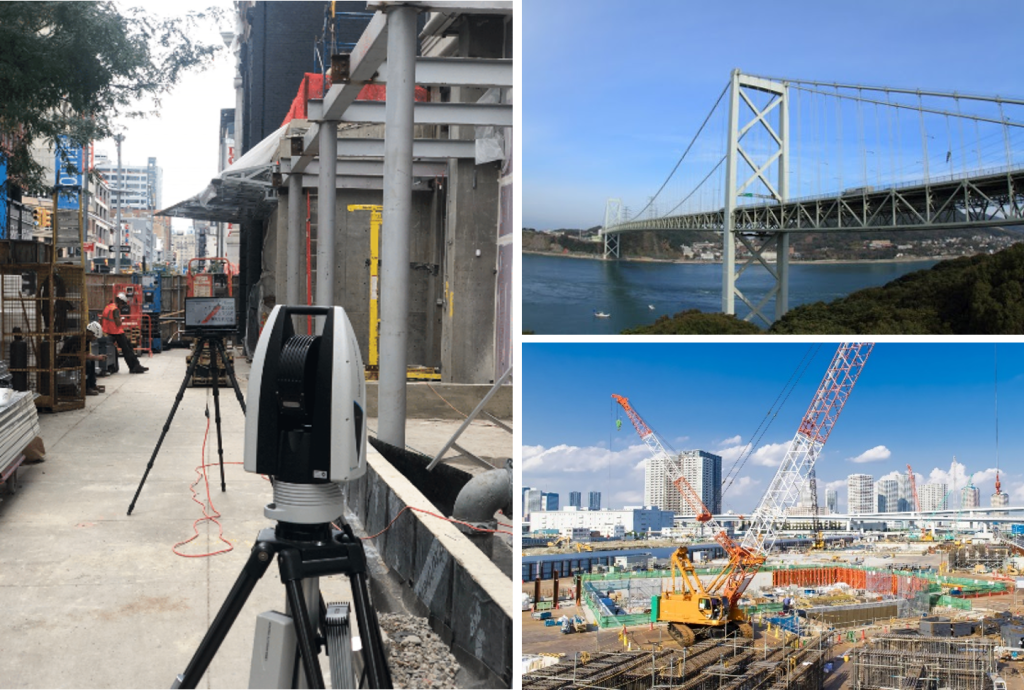
STEP1: Scan a large structure such as a bridge with a laser tracker.
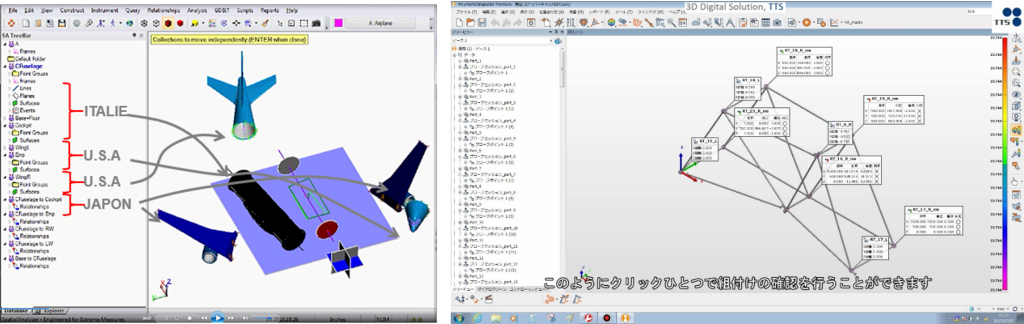
STEP2: Perform virtual assembly on the software and correct errors if there is any before its actual assembly.
(L: Aircraft / R: Steel framed structure)
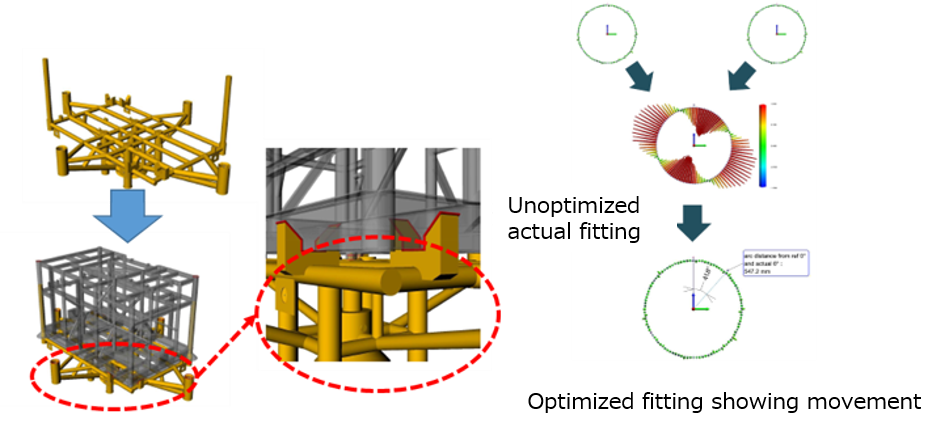
STEP3: Perform optimization in the software
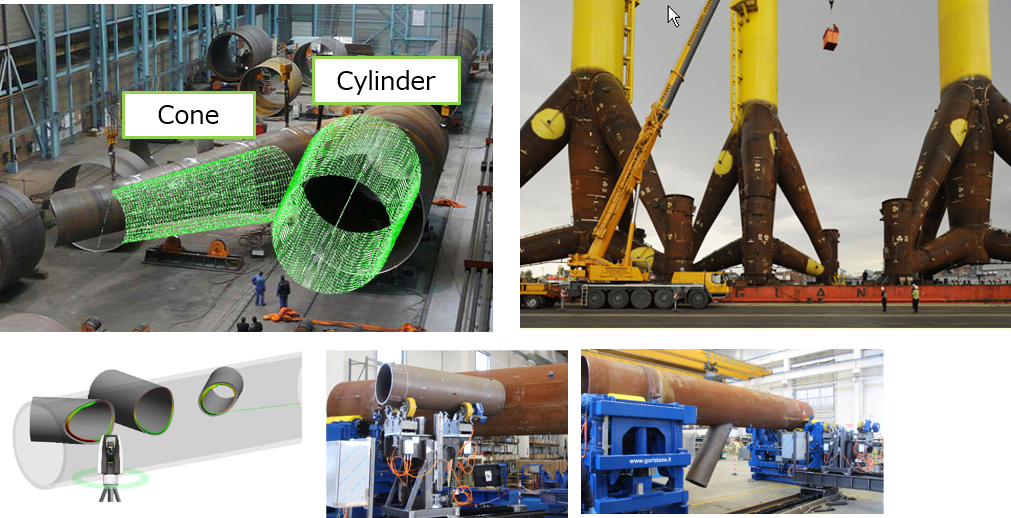
Case: Measure the scaffolding parts of the wind power plant to calculate the angles and intersections between the axes of the cylinder and cone, and make OK/NG decisions in advance. Measure the shape of the cut part of the component, perform a fitting simulation on the software, and make the necessary corrections in advance.
This shortens the adjustment process at the site and reduces rework.
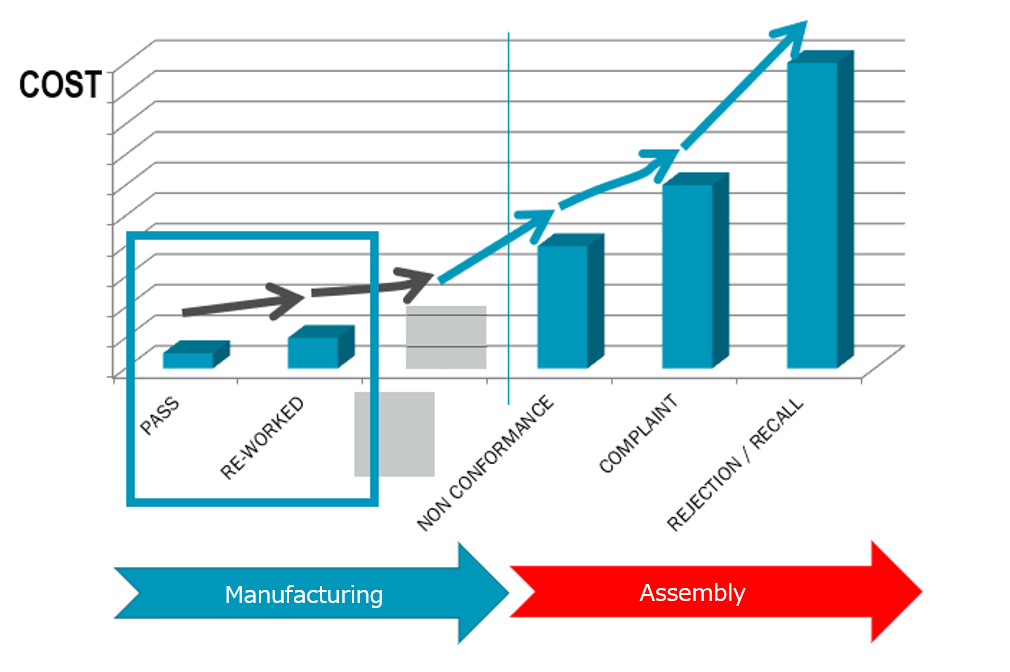
Tip: In the assembly of large structures, the later the process, the more costly it is to correct. It is important to identify and correct defects in the initial process.
System Configuration
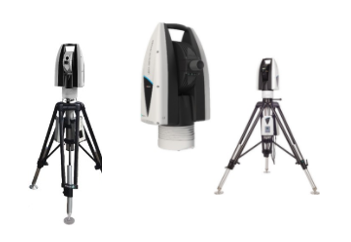
AT960 or ATS600
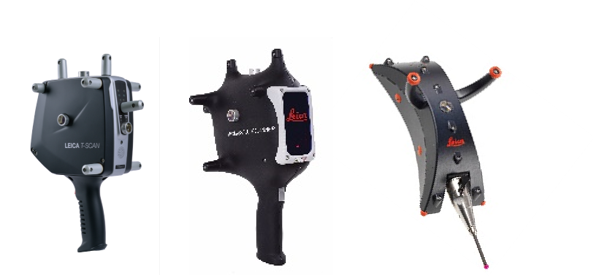
(only when surface measurement or probing is required)